Improving Through-Put by 75% without Increasing Manpower
02.01.2012
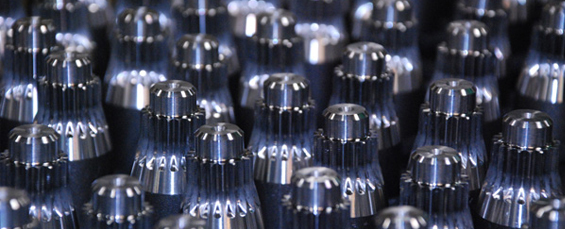
With more than 70 years in the industry, Mercury Marine has maintained its industry leadership position with constant innovation, foresight, and the use of superior technology. These characteristics are shown throughout Plant 4 in Fond du Lac, Wisconsin where Bill Cusick and Kurt Lefeber, Mercury Marine process engineers, produce high volumes of drive and propeller shafts for outboard and stern drive marine propulsion applications.
Unfortunately, lean operations and maximum levels of productivity weren't always a way of conducting business for Mercury Marine. By using a multiple-step process, shafts were produced by way of turning on a lathe, dropping the shaft out, taking it to a WWII vintage Barber Coleman hobbing machine (a very time-consuming, labor intensive method), cutting the spline, and then removing the part to a grinding operation, taking 3 min. in just turning alone. New Okuma CNC machine tool technology and the WTO hob assembly are doing away with some dedicated hobbing. Now turning and hobbing is done in one machine in just 3 min., 40 sec. Mercury Marine now has similar through-put and excellent quality with one machine performing the operations of two older machines.
Mercury Marine is now running an Okuma LB3000 EX BB MYW800 CNC lathe (M spindle with live tools; Y-axis with 5" of travel; W subspindle; 800 mm bed) equipped with a Westec overhead gantry for loading and unloading shafts, producing complete shafts in as little 3 to 4 min.
Okuma has a unique method of transferring the shaft from the main spindle to the subspindle utilizing a pneumatic pusher system inside the main spindle. When the gantry places a raw piece into the spindle, it goes to a backstop where there is an air cylinder with a piston. When the first operation is finished, to transfer the shaft to the subspindle, an M Code in the control (an auxiliary M function) fires the air cylinder which pushes the shaft out of the main and transfers it to the subspindle. With a long part and a small chuck, you'd have to move the part by a series of pulls by the subspindle. With this arrangement, the air cylinder facilitates the transfer to the subspindle.
Previously, the cell process had the blanks machined on a twin spindle LT10 Okuma lathe (without live tooling). The machined shafts would then be manually transferred to a Gleason P60 hobbing machine that was dedicated to cutting the splines. The new LB3000 EX BB MYW800 was put in place for added flexibility and as backup for the cell. Now a single operator runs both the existing LT10/P60 machines and the new Okuma lathe. Which means, an additional 75 percent output in the cell without an increase in manpower.
Mercury Marine's Kurt Lefeber says, "I looked outside some five or more years ago for a solution like this, and we had some manufacturers do some test cuts. The quality wasn't there, the cycle time wasn't there, and the capability really wasn't there, so we decided not to pursuit it. The Okuma machines have the rigidity to do the hobbing work, and that goes for the WTO unit as well- it's got to be able to hold the hob cutter. Previous styles of hobbing units held the cutter with the standard single mounted cutter where the hob end was not supported. WTO allows support on both ends of the cutter. Cutter life is better, spline quality is better than we were getting on the dedicated hobbing machines and the hobs last longer."
We offer a variety of ways for you to stay informed about our events, and to receive general Okuma updates. Fill out the form below to let us know the type of information you'd like to receive.