Low Foam Technology Solves Production Problems
02.18.2015
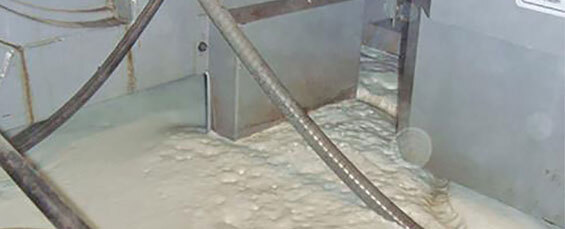
Coolant selection can make a big difference in how equipment operates. Just ask Jim Legg, general manager of LB Pipe & Coupling, Magnolia, Texas. LB Pipe had purchased and installed an automated cell from Okuma, which was the centerpiece of a new facility for automating the production of API couplings. The cell included a pair of Okuma 2SP-V60 machines with a ChipBlaster high-pressure coolant delivery system and a high-speed robotic arm.
At the initial machine startup, shaving cream-like foam billowed out of the machine and onto the floor, shutting down the high pressure pumps and creating a maintenance and safety nightmare.
The foam coming from the coolant delivery system was so severe that LB Pipe & Coupling had to keep a pallet of liquid absorbent on hand to capture the coolant that spilled onto the floor. The foam shut down the high pressure pumps.
A call was made to Jerry Peck, executive sales engineer for QualiChem, who drove 300 miles through the night to arrive on site the next morning. He assessed the situation and recommended Xtreme Cut 250C, a premium, heavy duty, semi-synthetic coolant formulated specifically to optimize tool life and surface finish in high pressure applications.
They charged one of the ChipBlaster machines with the QualiChem coolant and started up the production line. They were immediately able to begin increasing the pressure. After 7 hours of production at 1,000 psi, the machine running on QualiChem had no foam and no chip buildup. The other machine, running at 500 psi with the previous coolant, was overflowing with foam, and chips were still accumulating inside the chuck. The decision was made to immediately clean out the second machine and recharge with the QualiChem coolant.
“The result of changing coolant made a night-and-day difference in terms of better chip control and decreased downtime. LB Pipe was able to immediately run production at the machine’s full design capacity, which also improved tool life by 300 percent," says Rick Kimmins of Okuma.
“Shortly afterward, we invited QualiChem, as a metalworking fluid manufacturer, to join the select group of experts in our Partners in Thinc program. This allows us to leverage their expertise and knowledge to solve coolant problems experienced by our customers,” Mr. Kimmins says.
Glenn Frank, president of QualiChem, says his company has developed the Xtreme Cut 250C coolant technology to address the root cause of foam, which results in coolants that do not rely on defoamers as a band aid. QualiChem’s new coolant technology is said to result in a premium line of cutting and grinding fluids that can run at or above 1,000 psi in deionized water without foam.
To read more, see the full article as it appeared in the February 2015 issue of Production Machining Magazine https://www.productionmachining.com/articles/low-foam-technology-solves-production-problems
We offer a variety of ways for you to stay informed about our events, and to receive general Okuma updates. Fill out the form below to let us know the type of information you'd like to receive.