HAINBUCH Workholding: Innovations that Inspire
05.20.2022
In episode 33 of Shop Matters, join as Al Dopf from HAINBUCH shares his company’s passion for workholding and how their solutions can be used for various machining applications from ID/OD clamping to 5-axis machining. Also, learn how workholdings are evolving to be used with automation and being enhanced with smart technologies.
Connect With Okuma:

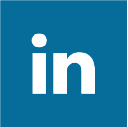
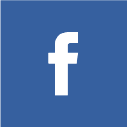

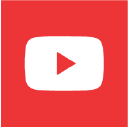
Connect with HAINBUCH Workholding:

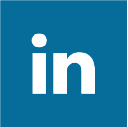

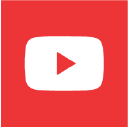
TRANSCRIPTION
Wade Anderson:
Hey, manufacturing world. Welcome to another episode of Shop Matters sponsored by Okuma America. I'm your host, Wade Anderson. Joining me here in the studio today, I've got Al Dopf from HAINBUCH Workholding. Welcome, Al.
Al Dopf:
Thank you, Wade. It's good to see you.
Wade Anderson:
Al, why don't you introduce yourself, talk us through a little bit of your career and what you do for HAINBUCH.
Al Dopf:
Okay, I'm the national sales manager for HAINBUCH. Been in the machine tool industry for a long time. In fact, been in the metal cutting industry, my first job in 1979 was selling plasma cutting equipment as a regional manager for the Carolinas and then eventually Virginia. I've worked for machine tool dealers. I've worked for machine manufacturers, worked for accessory companies, been in workholding now for about the last 15 years. And now I'm a national sales... I've been a national sales manager before for another accessory type company. The workholding part I'm passionate about now because I've been doing it a long time. I had a really good mentor that brought me along. So, it's exciting now, and it's exciting to lead another group of sales guys. And I have a very good quality product as well, and a good company to work for.
Wade Anderson:
Workholding is a fun part of machining. Back when I was an AE, running the machines, doing a customer process was one thing. Back then, a lot of what I did, I'd have to make my own fixtures, my own workholding, 6 point nest, that sort of thing. And for me, that was always the funnest part of any process because your brain is really engaged on how do I hang onto this part and work around and get the geometries, get the R&R that I need, the repeatability that I need on the part and things of that nature. It's so intricate and a fun part of the machining process. Tell us a little bit about the products that HAINBUCH... What is your sweet spot in the marketplace?
Al Dopf:
That's a good question. So HAINBUCH lives in the smaller diameter round part area. So, although we do specials, and we do a lot of large parts as specials, off the shelf things are in the 160-millimeter range all the way down to five, sometimes even as small as 3-millimeters. We do OD clamping, we do ID clamping, we do 2-jaw, 3-jaw, but our main thing is quick change. So, we're quick change at everything, but at the same time, we're selling tight concentricity. We're selling rigidity and we're selling flexibility. For instance, with a segmented collet or clamping head the way we call it, you have parallel clamping on a round part, but you're clamping 360 degrees of that part minus the vulcanization on it. So, unlike a jaw chuck which is self-centering, we have great radial clamping, and then also with a pullback chuck, whether it be ID clamping or OD clamping, you have axial drawdown or axial pullback and radial clamping.
Al Dopf:
So, you have a snug, snug grip on a round part, whether it be ID or OD. Also, unlike a 3-jaw chuck, you don't have to worry about centrifugal force. The effect of centrifugal force is much less because the actual body of a chuck is surrounding the clamping head, whereas on a jaw chuck, the jaws are exposed and they have a tendency to work their way out and lose clamping force at higher RPMs.
Wade Anderson:
You mentioned that you guys really specialize on the round stuff. I'll give a quick story, a story I always like to share about working with HAINBUCH and our Partners in THINC facility. We did an open house several years ago, we called it the Winter Showcase. What I try to do is team up different partner companies together to come up with something, a problem that they see in the industry, things that they see customers struggling with, or new technologies that they want to introduce, and work together as a group of five to seven companies to develop whatever this process looks like. I don't tell them what machine. I put the group together, let them come up with it. And then they come back to me and say, "this is the part, or this is the solution we want to show and here's the machine that we would like to do it on."
Wade Anderson:
And having HAINBUCH in the mix, I was just automatically expecting it was going to be a lathe or one of our multifunction machines. We call it a MULTUS machine. And instead, when the team leader came back to me and said, "hey, we would like to get one of your small 5-axis machines" or, sorry, it was actually an M560 with a Nikken fourth and fifth rotary table on it, it floored me because I just automatically assume you guys go on lathes. And instead, you guys came back and said, "yeah, we're going to use one of our collet systems. We're going to hold a part in a different manner." And the part actually had a bore on it that you were able to grip with an ID collet, but there was no turning on the part whatsoever. It was a 5-axis milled part, but it was just one of those things. You paint yourself into a corner sometimes or get a preconceived notion. I had a preconceived notion you guys would be on a lathe and, instead, you came back and said, "yeah, put us on a mill. We want to hold this 5-axis part."
Al Dopf:
That's interesting because we do stationary workholding with everything that we have as far as... We have clamping heads for OD clamping and ID mandrel sleeves for ID clamping for stationary workholding. And we have manual clamping for stationary workholding. But it's interesting, we do just as much stationary... Well, we don't do just as much. We can hold round parts in stationary workholding just as well. And all the adaptations that we have for quick change, we can change a stationary chuck from OD clamping to ID clamping to 2-jaw, 3-jaw. We have a magnetic chuck that we could put on. The only thing we can't do on stationary clamping is hold between centers and put a face driver on it, for obvious reasons.
Wade Anderson:
So, let's talk about quick change. And that's the strength area when I got to know HAINBUCH as a company, was the quick change stuff. That's what we showed at IMTS a couple of times, a lot of the systems we've had in Charlotte on the machines and things that we've done in the field with customers, they're all around a quick change solution. And when I look at how customers produce parts, I go back to when I was an AE doing time studies back in the 90s. We would win and lose projects based on cycle times of parts. But most of the time, those were on high volume, high production type stuff. In today's world, we're not seeing too many people... You've got certain OEMs or top-tier suppliers that are landing these large production runs, but over 80% of our business at Okuma is the job shop area.
Wade Anderson:
Well, those guys aren't running the large volumes, they're doing smaller quantity volumes and a lot of changeovers, which requires a lot of setups. Now all of a sudden, your cycle time, when you put math to it, you can have a longer cycle time on a machine that has a much faster rate of doing changeovers, and you can be much more productive and win a lot more money at the end of the year than what you do off of if you're just trying to focus everything on what your cut time is, what your cycle time is. So that quick change is such a vital, important aspect of being able to go from part A to part B or part A to part C quickly. The faster I can do that, the faster I can get my spindle back cutting parts and making shipments where I make money at that point.
Al Dopf:
Yeah, we talk about that all the time because setup time can take hours in some instances. So, with a clamping head, we have the quick change. For OD clamping, we could change a clamping head in 15 seconds to go from one diameter to another. But we can also do Op 10 on an OD clamping, and then Op 20 might be ID clamping. In a matter of a minute, a minute and a half, we can use the same chuck and put an ID mandrel onto it. Short runs, if they need to put something on that they need a 3-jaw chuck, on that same chuck, we have a 3-jaw chuck adaptation that can go on. We can do face driving and hold a part between centers in just a matter of minutes.
Al Dopf:
And then we have another thing called our centroteX where we can change an entire chuck, anyone's chuck, in less than five minutes. The whole chuck. And that's usually something that takes hours because you have to unbolt a chuck, and chucks are heavy, and it's not even safe getting in there and grabbing a chuck. But with our centroteX system, we have the part, we'll call it the flange, that goes onto the machine, onto the spindle nose. We mount that during installation. We indicate it and get that right on, very little runout. And then it repeats every time. You don't have to worry about that again because then you have the base plate. And then every chuck that you have will have another adapter that goes on it.
Al Dopf:
And it's just a matter of taking a turn and a half on the bolts on a chuck. It's got the bayonet system. You give it a 15-degree turn, it comes off, and you're ready to put another one on in a minute and you don't have to indicate, you don't have to tighten all the bolts. It's just on. And you can be confident that the runout is going to be within eight microns or less. That's a huge savings.
Wade Anderson:
I'm used to seeing that on mills for zero-point workholding. You have a base plate and a receiver, your vice or fixture goes onto a receiver or a base plate that goes into the receiver. So, you're taking that same concept and adapting that to a lathe application. So, if you've got an A2-6 or an A2-5 or 140 flat nose, you would have an adapter plate that goes on that spindle nose, and that would be the receiver. And then your base plate goes on the back of whatever chuck and allows for the quick change.
Al Dopf:
That's so interesting because I never compared it to a zero-point clamping system, but it's close.
Wade Anderson:
I'm more than a pretty face, pal.
Al Dopf:
That's interesting. Actually, a zero-point clamping system can be a hair faster, too, because you just pop it right on and pop it off. But think about the amount of time you're saving, and just like a zero-point clamping system, we can also do this from one machine to another machine. With these short runs, if you have a machine that has some open time and it has our base plate on there, you can go ahead and take a chuck from one machine and a job that one machine normally does and take it over to the machine that's idle and put it on there. That way you could be making parts on both machines, too.
Wade Anderson:
That's an excellent point.
Al Dopf:
Again, it's so fast because the amount of time that you spend undoing bolts, and then the most important thing is getting it indicated in again.
Wade Anderson:
Your concentricity and-
Al Dopf:
What you're doing there too, you take the bolts off, you tighten a new chuck on there. You put your indicator on, you loosen the bolts a little bit, you get your orange plastic hammer and bang on it, and you get it a little bit too far off, and you go back the other direction and go back and forth. Depending on the person doing it, that alone could take 45 minutes, taking the chuck off and putting it on. I normally say to take a chuck off and install a whole new chuck could take three or four hours. And we can do it in five minutes. It takes time to put the original base plate, we'll call it, in the receiver.
Wade Anderson:
Your initial setup?
Al Dopf:
Yeah, but once that's done, it's fast. And if you're using our chucks on it, our OD or ID clamping chucks, you can still change the diameter of parts very quickly with the... I call it the pistol grip, but the collet change fixture that you put it on. And even if you're holding from the ID, you can still change those in a minute. So, we're big on quick change, but at the same time, we're big on repeatability with quick change and not having to re-indicate.
Al Dopf:
So again, we're holding concentricity with radial clamping and axial drawdown. We're holding a rigid part, which prevents chatter, which gives you better surface finish, which makes tool life last longer. So, there's a lot of things that we're about that completes a system too on a machine.
Wade Anderson:
Can that tie into automation? Are you seeing any of that technology find its way into automated cells?
Al Dopf:
Absolutely. For smaller diameters, we have this centroteX system that we use for changing entire chucks. And we have it where you can change out chucks using a robot. I'll back up a little bit. We can change a clamping head or segmented collet from one diameter to another with a robot. We can also change the endstop or workstop with a robot, too. So, I didn't mention that yet, but that's important because that's custom, and we're making custom endstops, and we can do custom clamping heads, too. But when you're using automation, you usually need air sensing for part confirmation, and that's part of the endstop. So, we'll need a different one for each part we're going to do, too. We can change those with a robot. Then we can change the clamping head with a robot.
Al Dopf:
Then we can also change the adaptation to go from OD clamping to ID clamping with a robot. Then the next step is we can change out the whole chuck with a robot, too. It's the smaller diameter ones though. The robots do a A2-5 and A2-6 spindle nose range. Anything bigger, we haven't gotten to that yet. But it's interesting that with automation the way it is right now and short runs, you could have lights out, unattended operation with a machine and do a couple different operations on one machine with different types of clamping or different diameters, different parts, all completely unattended.
Wade Anderson:
Right. We did a cell several years ago, and we actually have one in Japan at one of our Dream Site facilities. You're familiar with the FMS system on mills?
Al Dopf:
Yes.
Wade Anderson:
Typically, you have horizontals tied into Fastems or another brand FMS system, which is basically a big shelving unit for anybody that doesn't know what an FMS system is. It's basically a big shelving rack system. And then you have an elevator that will feed the pallet in and out of the horizontals or 5-axis machines. But we've seen that on lathes now, and instead of the parts being in the racks, it's all the chucks, all the collets, and all the central pieces or the base plate type system. So, the robot, instead of feeding parts in and out, they're going up and grabbing the workholding and changing the workholding out and basically making a... I don't know if they're going to use that same terminology or not, but basically making an FMS system for a lathe, only the FMS is full of different types of top tooling, different types of workholding.
Al Dopf:
Right, and that's basically what we're doing when we change our workholding, but we've also taken it another step too because now we have what we call our TOPlus IQ chuck, which is a smart chuck with embedded sensors in it as well. So now you have unattended lights out operation, you're changing these chucks with a robot. But let's now get some data from these chucks and be able to make some adjustments on the fly without an operator there. With embedded sensors, we can measure clamping pressure, we can measure machine RPMs. So, we can look at if there's any loss of clamping pressure during the night. We know about it, and we can send that information to a machine controller where adjustments can be made on the fly. Or the information we send to the controller, at least it can be analyzed and they can say, "oh, maybe the tool is wearing out," or something like that.
Al Dopf:
Because the things that we can measure... We can measure clamping pressure, we can measure spindle speed and RPMs. We could measure, if it's an Op 20, we can measure the size of the part, the diameter of the part by clamping on it. So, if you see it's going the wrong direction, an adjustment can be made. Or you could say, "hey, maybe the tool is wearing out," or something like that. We can measure vibration, so if there's chatter from the tool. We can also measure, instead of having air sensing for part confirmation while the parts are being changed, we could have sensors there, too. That eliminates all that plumbing, that eliminates a rotary union for air. This data is transmitted to the controller non-contact because obviously the part is turning.
Al Dopf:
That's something that really works well in a partnership program like we're part of. Because we can give you the data, but what you do with the data is a whole other thing. Even from the tooling, you could put a chip on a tool holder, you have smart tooling, it's all part of Industry 4.0 and the direction we're all going. We're doing our share on that, but standardization might be important. Partnering with our other companies like we do with you is also important too because you have the controller, we just have the data that we're giving to you and it has to be analyzed. Sometimes it could just be used for history, so you could follow this part and you know what happens eventually so you can predict changes at different times, too. So, it's exciting.
Wade Anderson:
I wish I'd have thought through this more when we chatted about you coming to be part of this podcast. Earlier today, we had Datanomics and Caron Engineering in here, and a big part of their talking points was data and collecting it and then not just collecting it, but what do you do with it? How do you use that to make your manufacturing process better? I should have had you sitting beside me and had all three of us talking because that is a direct tie-in to exactly what Datanomics and companies like yourself, Caron Engineering... We can extrapolate a lot of data off the process, but then what do you do with it? That's where a company like Datanomics and other people can come in and feed that to help you make informed decisions about your manufacturing process.
Al Dopf:
Absolutely. And that part of the industry is changing so fast. It used to be where... I'll back up. HAINBUCH had this smart chuck made 10 years ago, but no one could use it.
Wade Anderson:
The market wasn't ready.
Al Dopf:
Right, so we put it on the shelf, and now that the market is ready, we took it off the shelf, we blew the dust off it, and now we have a product. But the original one, the data was transmitted via Profibus. Slow and old-fashioned, and that's not the way to go. Now that we have this contactless transmission of data and controls and other companies are getting more involved in this, this is the direction of Industry 4.0. That's one of the hottest things. My thing right now is we've got to keep up with the times, we have to automate because things are changing. And it used to be that workholding was the slowest part to change. Machines got so much faster. Machines had direct drive. The inertia from stopping and starting and everything required good quality workholding.
Al Dopf:
Tooling changed and it was cutting so much faster. Workholding hadn't changed a whole lot. One thing about HAINBUCH is, our R&D department is busy all the time. They're looking at new things. We have new things on the drawing board all the time. And that's what I love about our company. It's looking to the future as well. We might have gotten a slow start here in the U.S. compared to some of the others, getting here and getting our name out. But now we're getting our name out. We're known as fast, quick change. We're known as very rigid clamping and holding tight tolerances and repeatability and accuracy. So, we're there, and it's exciting to know that over in Germany, we have an R&D department that's working hard to keep up with the times and constantly make changes and look for new ways of holding parts better.
Wade Anderson:
Excellent. You had mentioned earlier about a carbon fiber chuck.
Al Dopf:
We do have a carbon fiber chuck, yes.
Wade Anderson:
See to me, stuff like that, that's interesting technology. And I don't know that everybody's ready to go that route yet, but just to think again, where are we going? What's going to be on the market five, 10 years down the road?
Al Dopf:
I agree. Our carbon fiber chuck, the reason you have that is light weight.
Wade Anderson:
Spin it up and down really fast.
Al Dopf:
I love holding it. We have one in Germantown, Wisconsin. I love handing someone a heavy chuck and then handing someone this carbon fiber chuck, and it's light as a feather.
Wade Anderson:
And that goes into a payload capacity as well for a robot. If you're trying to do a collaborative robot solution where you're trying to implement something yourself, what a great way to look at, can we get weight out of the process?
Al Dopf:
Changes the size of the robot that you have to use. The robot can go a little bit quicker because the starting and stopping and then the inertia of a heavy chuck is a lot harder. With something real light, it's even easier. What we have to do is get everyone competent enough, and you look at a lightweight chuck like that, and it doesn't have the gripping force of a big, strong, steel chuck, but there's a place for it. The lighter materials, plastic material too. So, there's a place, we need to just get that out, but thank you for bringing that up because it's another one of our newer-type innovations that we have.
Wade Anderson:
Hopefully, I didn't speak out of turn. Is that a product that's on the market? If somebody had the right process and the right part is that-
Al Dopf:
Yes, we have a part number. We have one in Germantown, Wisconsin. I believe it's a six-inch chuck maybe, I'm not sure. But yeah, we have one, it's got a part number. It's something that we manufacture. It hasn't taken off that much yet, but it will.
Wade Anderson:
Will you guys be at IMTS this year?
Al Dopf:
Definitely, we're looking forward to that too. In fact, the news that we're hearing now, the mask mandate is being lifted in Illinois. Just from your marketing department in the last couple days from meetings that they had, it sounds like they're on track with attendees of 2014, 2016 IMTSs, which were fine because 2018 was a record year. And I think people are doing the wait-and-see type of thing. I'm excited. I've heard the exhibitors are filling the place up, too. There might even be a few more changes there if people are doing the wait-and-see, but I'm excited. I'm optimistic that it's going to be a good-
Wade Anderson:
From Okuma's perspective, we're all in. We're going into it just as we would any other 2014, 2016 type years. We've got a really good crop of machines going, and I had to submit my personnel list and budget of who I'm sending from my team to go up there. But I'm looking forward to it. I think there's a lot of people last year... Or last, I always call it years in terms of IMTS, it's funny how you do that in this manufacturing world. But two years ago, we didn't do a physical IMTS with the pandemic and everything. So I think there's some people ready to get back in front of people again and machines and seeing technologies. And I think it's going to be a big show for us.
Al Dopf:
Right, and I agree. It's been four years, so people like you and I, who can count years that we've been in the industry by how many IMTSs we've worked. We're excited to get back in. There's been a lot of changes in the last four years as well, too. There's a lot of new people in the industry, too. So, I think that will be interesting for them. I think people are excited. End users are doing things.
Wade Anderson:
My stomach's growling, it's going to come across on film, I think.
Al Dopf:
Even manufacturers are making different types of parts. You look at the different industries. In four years, the automotive industry has really changed over to electric vehicles.
Wade Anderson:
Yeah, what a great point.
Al Dopf:
And even aerospace, materials are changing. But yeah, the automotive industry going from gasoline-heavy has changed a lot in the last four years.
Wade Anderson:
The way those parts are manufactured. And it's got us looking at what machine tool designs have to change to address changing markets? As we're looking at how the machine tools change, that's got to affect you guys on how does the workholding side of it change?
Al Dopf:
Another thing that HAINBUCH specializes in, we're really good at holding gears. We can put a clamping head, we could profile the gear in a clamping head and actually locate and grip on the pitch diameter of a gear. And we can hold gears on an ID and have plenty of room for a hobbing tool to get in there and cut the gear teeth. So, after a gear goes to heat treat, it comes back, and one of the final stages is touch up that ID bore and make it in direct relationship with the pitch line. So, if we can clamp on the pitch line and locate in the same place and do that, ID bore is in direct relationship with it. The reason I bring that up is because gears is one of the places with electric cars is going to change. There are less gears in an electric car than there is in a transmission, but there's still a good amount of gears, and some of them are at each wheel.
Al Dopf:
And there's still steering, there's still things like that. There's still a good amount of gears in electric vehicles that we're still excited about the automotive industry for that point of view, too.
Wade Anderson:
Well, Al, thank you so much. Been a great chat with you. I appreciate you taking time to come in and join us.
Al Dopf:
Thank you, Wade. I enjoyed it. It went fast.
Wade Anderson:
It does, I tell you. So, if customers are listening and they want to learn more about HAINBUCH, how do they reach out to you?
Al Dopf:
HAINBUCH.com
Wade Anderson:
Alright, easy enough. Spell that for them.
Al Dopf:
H-A-I-N-B-U-C-H
Wade Anderson:
Perfect. And thank you for joining us. If you have any comments, questions, or ideas for future podcasts, please reach out to us. Be sure to check out all of Okuma's social media channels for other video content, as well as machine information. Until next time, we'll see you then.
We offer a variety of ways for you to stay informed about our events, and to receive general Okuma updates. Fill out the form below to let us know the type of information you'd like to receive.