The Latest in Cutting Tools and Digitization
07.01.2022
In episode 36 of Shop Matters, learn great insights from Sandvik Coromant’s John Winter as he discusses the current marvels of cutting tools and ways to extend your tool life. Also, discover how Industry 4.0 and data play a key role in understanding your machine and tool availability while increasing transparency and the opportunity to optimize your production processes.
Connect With Okuma:

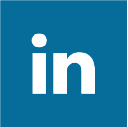
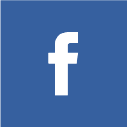

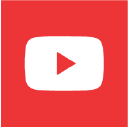
Connect with Sandvik Coromant:

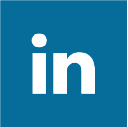
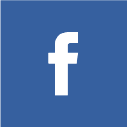

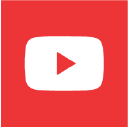
TRANSCRIPTION
Wade Anderson:
Hey, manufacturing world. Welcome to another episode of Shop Matters, sponsored by Okuma America Corporation. I'm your host today, Wade Anderson. And joining me today, I've got Sandvik and John Winter from Sandvik. So welcome, John.
John Winter:
Thank you, Wade. I want to say thank you for inviting us here to Shop Matters. This is a great opportunity to showcase Sandvik a little bit along with Okuma.
Wade Anderson:
Yeah. It's great having you here. I've been trying to get Freddie to come on several times, but I think he's camera shy. He doesn't want to step up in front of the mic.
John Winter:
No. You put a camera in front of him and he gets a little scared, but he'd do a good job.
Wade Anderson:
Oh, yeah. Yeah. He's a good guy. So, for all you listeners out there that don't know, I manage our Partners in THINC program at Okuma and spend a lot of time with a lot of different partner companies, and Sandvik, for a long time, has been one of our most active partners. They have a guy, Freddie Wilson, who I was just talking about, that practically lives in the office. He's there a good bit. But John, tell me a little bit about your role and how long you've been with the company.
John Winter:
All right. Again, my name's John Winter. I am the product manager for Sandvik Coromant. I also manage the eastern product management team for the U.S. So, I cover some of the product, but I also have a team underneath me that covers the whole product offer for Sandvik Coromant.
Wade Anderson:
I've been with Sandvik now 16 years and been loving every minute of it, to be honest with you. It's a great company to work for.
Wade Anderson:
Yeah. We've had a strong partnership for a long time. And why don't you tell me a little bit about Mebane and the new facility and how our relationship works up there.
John Winter:
Well, we have a new training center in Mebane, North Carolina, attached to our manufacturing facility. So, we can also showcase our product and the manufacturing capabilities we have within our own building, but we also have two Okumas on site where we can do machining demos, power skiving, turning, and all these are tied to our center where we can do customer projects. We can do training. It's a great opportunity for people to come and see what we have to offer at Sandvik Coromant.
Wade Anderson:
All right. So, you mentioned a couple of things. I always try to keep my ears peeled for different keywords that people throw out. So, talk about power skiving. Describe what that is.
John Winter:
So, power skiving is taking a multitask machine, like a MULTUS, and you're actually cutting the gear teeth without having a form of like a hob. So, you're able to use the B-spindle and the spindle on the machine and position it accordingly, and actually cut your gear teeth extremely fast. So, a lot of places where maybe you've got maybe ten parts or 20 parts or prototyping where you don't want to have the expense of buying a hob for some gears, we have the ability to do that right on the machine.
Wade Anderson:
All right. Fantastic. So, let's take a minute and kind of step through a couple of products that we work with you guys a lot on. We use a lot of these tools in both the Partners in THINC facility, and then obviously, I know you guys do in Mebane as well. But let's talk a little bit about the MH20 and what that mill is.
John Winter:
So, MH20 is a high-feed mill. It's the latest high-feed mill concept from Sandvik Coromant. It's designed specifically for pocketing. It can be an aerospace frame. It could be aerospace engine or even die mold where we're doing deep pockets, and you want to remove metal quickly.
Wade Anderson:
So, I hear that word a lot, high-feed milling or high-feed mill, I should say. For anybody that's not familiar with that, what is high-feed mill? And are there materials or certain types of applications that is not a good fit for?
John Winter:
Well, first of all, high-feed milling is basically taking the lead angle of the insert and tipping it very steep, allowing us chip thinning. When you look at a milling cutter, the inserts are designed for a certain chip load, and usually, with a 90-degree cutter taking 75% of the cutter diameter, your feed rate matches your chip thickness. So, if you're doing five thou a tooth, that chip thickness is going to be five thousandths. With high-feed, we're actually going to take and tip that 90-degree lead angle and make it maybe 20, like the DS20, so the depth of cut's a little bit lighter, but now we've thinned that chip out. So, in order to get the chip thickness that we need of five thousandths, your feed rate's going to be extremely higher, allowing us faster metal removal rates by thinning the chip out.
Wade Anderson:
Okay. And what does that do from, like you say, it's used a lot in pocketing. What's the benefit? Is that from a corner standpoint, coming into corners?
John Winter:
It's from the standpoint of getting a very fast metal removal rate. And the milling cutter's actually designed for more pocketing. We have a geometry that gives us clearance. We're not pinching chips against the shoulder as you go down in the pocket, giving us better evacuation of the chips. So, we get a better finish on the pocket, and we also get a stronger edge line because of that and gives us a better tool life.
Wade Anderson:
Okay. What about drilling? Talk about some of the newer drilling technologies that you've got.
John Winter:
Well, we've just come out with a DS20. This is a deep hole drill up to seven times D. Typical insert drills only go about five times diameter. Well, this one can actually go seven times diameter. It's got inserts that are four-cornered each, so you're going to have four corners on one insert. The outboard insert is actually double-sided, so you're going to have two corners on one side of the insert, two corners on the other. And it's kind of got a little bit of a dog bone shape to give us stability in the cut. The inboard insert is going to be square, and so you'll index that truly around to give you all four corners.
John Winter:
Now with the DS20, what we've done is taken that drill, and when you look at an inserted drill, the outboard insert's going to create a certain chip formation, and the inboard insert's going to do a different type of chip formation. So, what we've done is we've looked at that flute design and optimized it. So, the flute is designed to allow the chip evacuation but also give us the most rigid drill body possible. That's why we're able to go seven times D with this drill.
Wade Anderson:
All right. What would be some of the key applications that you've seen so far using that?
John Winter:
A lot of oil and gas components when you look at valve bodies where you're having to go through a flange, very large valve bodies, you look at diaphragm valves or even gate valves where you've got a very deep drill that you got to go through. So, it works extremely well in the oil and gas.
Wade Anderson:
Okay. Many, many years ago, I used to do a lot of tool and cutter grinding. I worked for a tool and cutter grinding company, Huffman Corporation. And one of the very first jobs that I worked on was actually doing some OSG... Or I believe it was either OSG or GAR tools, but we did one of their tool and cutter grinders back in the early '90s. And over the years, I hear a lot about different types of coatings. And back in my days, cutting end mills, we were just cutting the geometry. I didn't really know that much about coatings. Now, just about every material that you're getting into, and you start talking to the tooling guys, they all start talking about coatings and different types of applications. So, help me out, help me understand more of the coating process? And how do you know what coating is right for what type of process that you're looking at?
John Winter:
Well, usually, there's two different types. There's a CVD, which is chemical vapor deposition. And the chemical vapor, you can lay them on a tray and coat the whole insert, and it's multi layers. Then you got a PVD, which is a physical vapor deposition, and here you actually have to hang the insert. So, one easy way to tell if you got a CVD versus a PVD insert you'll be able to see raw carbide, uncoated carbide. That will tell you it's a PVD-style insert, and that's usually a thinner coating. We have a coating called Zertivo™ that is in our PVD arsenal, especially in the milling. It actually has a very good bond to the substrate or the carbide, giving us better tool performance.
John Winter:
Now, when you look at the CVD coatings, there, we have Inveio™. Inveio is a multi-layer coating where we've actually aligned the crystal structure of the coating for a stronger coating. And then that alignment of the crystal structure, it's kind of like an egg. If you take an egg and lay on its side and put some pressure on it, it breaks pretty easy. But if you put it across the points and put some pressure on it, it's harder to break that egg. And that's kind of the crystal structure. We've aligned it where we have the strongest part of the crystal that's aligned with the cutting action of the insert, giving us a stronger coating, better tool life. This also helps pull heat away from the cut zone to give us better tool life and keep that substrate cool, so we have better resistance against plastic deformation.
Wade Anderson:
Is there any type of cutting data that you have when you are advancing to this newer technology of how much extra tool life or time in the cut can you get out of these newer coatings?
John Winter:
Well, we have the second generation Inveio coating, which is grade 4415 and 4425. The difference between those two coatings when you look at the isostructure, you look at a P25, and that's going to be kind of where you start. You don't know if you have interrupted cut. You may have some scale or forging. That P25 gives you good resistance that's a little bit of out of cut out around. The P15 is a little bit harder of a substrate, which now, if you've got great continuous turning, that's when you get the most tool life. So, when you look at those with those new 44 series grades that we've just launched, we're seeing, on average of, about 20% improvement in tool life.
Wade Anderson:
Wow.
John Winter:
Now, if you optimize the cutting data, which means you're going to look at your speeds and feeds and optimize your surface footage and your feed rate, you can get even better tool life. And tool life and productivity is money.
Wade Anderson:
Sure. Absolutely. I think that's something that is many times overlooked. I deal with the machine tool side of things a lot, and the cost of ownership and the amount of money that you spend on perishable tooling a lot of times never enters the equation on the upfront purchase costs and things like that. So, a better quality machine and a better process overall helps that perishable tooling cost on your budget every year.
John Winter:
Yeah. And the other thing to keep in consideration if you're buying a new piece of equipment is you really don't want to put old tools in a new machine. When you look at that mounting old tools or even spindles, that can cause damage to the spindle if you've got pockets or wear on that interface. It could cause some issues. So, you should always look for the best tool and the best machine in order to optimize your process.
Wade Anderson:
That's an excellent point. We see that on a weekly basis almost. Somebody will buy a brand new, beautiful piece of equipment, and then they're dragging out tool holders that were laying in a cardboard box in the back of the shop for the last 20 years. And kind of makes you scratch your head sometimes. But those are excellent points. If you're going to put the investment in to have a new process, really do it right from the start. I'm a big fan of Dr. Edward Deming. And one of my favorite quotes was always, "Quality always costs less in the long run." So, you may pay a little more upfront for a higher quality process, but it'll always cost you less in the long run. You'll make more money off that better process.
John Winter:
Yep. Do it right from the start, like you said.
Wade Anderson:
Yep. So, as you were talking about coatings and heat coming out of the chip, it made me think about coolant and kind of going back to whether it's some of the turning applications or milling, you talked about your high-feed mill, in different applications, do you have a preference on coolant, of whether to use coolant, MQL, cutting dry, using air, things like that? What do you typically see or recommend?
John Winter:
When it comes to turning, I'm always with the coolant unless I have a very heavy interrupted cut. And we've designed new tool holders with over and under coolant. We've actually seen a huge benefit to getting coolant to the backside of where we're cutting. Keeps the substrate cool and gives us even better tool life and performance. Everybody's always put it on top thinking that, "I cool that chip real quick, it helps it to break," which is true, but with modern chip breakers, maybe I need to keep the insert cooler, and gives me a better tool life. So, we're finding that that under-coolant is key when you look at tool life and capabilities in turning. Now, when you look at milling, a lot of times because of the milling cutter’s in and out of cut, I will probably run dry, but there's plenty of applications if you got long cut time that coolant can help flush the chips away, so you're not re-cutting chips. And we have, through the tool, inserted mills that will flush the chips and keep the edge line cool.
Wade Anderson:
Okay. All right. Good points. How involved are you with Industry 4.0 and the whole digitizing of manufacturing, let's say?
John Winter:
Well, Industry 4.0 is one of the aspects of where Sandvik Coromant is going. We have what we call Machining Insights. And Machining Insights basically ties into the machine control, looks at all the sensors that are on the machine already when we look at speeds, feeds, vibration. And we take that data, analyze it. And based over time, depending on the parts you're doing, we can look at the process and help control the machine to make sure, "Do I have downtime? For what reason? Insert changes or breakage..." And we can monitor that. And over time, we build a database that helps you optimize your machine tool just by analyzing what's going on.
Wade Anderson:
Okay. That's a big thing. We can collect a lot of data but trying to find what's the data that's going to be useful for customers' processes and what do you do with that information. So, I think a lot of what I've seen so far from the insights that you guys are doing, it's applicable to the real-world cutting, the real-world manufacturing, and a lot of times in real-time. So, you guys are monitoring tool life, vibrational tool holders, and things of that nature?
John Winter:
We monitor that, but we also have connected all our manufacturing facilities globally. So, we can actually look at machining insights and see what's going on in Gimo, Sweden, or see what's going on in Mebane, North Carolina, based off of what... And each machine's tied to it. So, you can see each individual machine, and we're analyzing all this data to optimize our processes also.
John Winter:
Now, you mentioned what about actual cutting? And we have Silent Tools Plus. Now Silent Tools Plus is more of a boring bar application. One of the big ones that we do a lot on is you look at landing gear for aircraft, very expensive component. And when you're in that, boring the ID of that you can't see what's going on and so you're relying on the operator and the years of experience and understanding what's it sound like. Well, now we can actually monitor that. We have a vibration monitor. We have a heat monitor that monitors the temperature of the bar. And we can look at all these parameters and determine, "All right. Am I wearing out? Am I good? Do I need to stop before I damage the part or damage the tool?"
Wade Anderson:
Okay. And all that is communicating to the control via, is that a Bluetooth connection? Or how is that information being transmitted?
John Winter:
It's being transmitted through Bluetooth. We have a tablet that allows you to monitor that. And the other cool thing on it, when you look at a boring bar, and you try to set your center line, we can actually rotate the bar and see the angle that we're rotating that bar on the tablet.
Wade Anderson:
Oh, no kidding.
John Winter:
So, you can actually set that to zero right outside the machine, lock it down, and you're good to go. Now, we've also included that into driven tool holders. So now we've got driven tool holders that look at vibration and heat within a driven tool holder to make sure that we're not going to have any damage to the tool holder itself. So, over time, it'll trigger you, "You need to maintain this tool holder before it becomes an issue." So, you monitor all that data.
Wade Anderson:
Yeah. That's great. So, you can get ahead and plan for downtime. You can plan for the maintenance and work that into your schedule rather than dealing with a catastrophic failure. All right. Excellent. So, that's great information, John. So, if somebody wants to learn more about the digital aspect of the work that Sandvik's doing or just learn about your products in general, what's the best way to get in touch with you?
John Winter:
You can go right to sanvikcoromant.com. There you'll find product information. You'll find information on MachiningInsights, Silent Tools™ Plus. We also have a CoroPlus® Tool Path, so we have the ability to create tool paths. It's not a full-blown CAM package, but it'll create specific tool paths for your needs. We have PrimeTurning™, which is high-feed turning. We talked about high-feed milling. So, Tool Path will give you the path that you need for high-feed turning with CoroTurn® Prime. It also gives you a new threading cycle that we've come out with called OptiThreading. A lot of times when you look at threading applications, you struggle with chip control. So, what this does is it actually creates a sine curve tool path. So, we're actually bouncing the tool in and out of cut, mechanically breaking the chip. And then that last axial turn is actually going to be a straight path, but the path right before has already created that thin to thick chip formation, giving us chip control on the last path.
John Winter:
So, a lot of great things to see, not only Industry 4.0 but the new products. So, come check our website out.
Wade Anderson:
Awesome. Very good. Well, thank you for your time today. And thank you for joining us. If you have thoughts, questions, ideas for future podcasts, please reach out to us. You can find me on LinkedIn or reach out to us on the okuma.com website. Be sure to check out all of our social media channels for more information and video content.
We offer a variety of ways for you to stay informed about our events, and to receive general Okuma updates. Fill out the form below to let us know the type of information you'd like to receive.