Institutions Collaborating to Improve Manufacturing
07.15.2022
On episode 37 of Shop Matters, Wade Anderson sits down with manufacturing experts from OPEN MIND and Oak Ridge National Laboratory to discuss the latest innovations in hybrid manufacturing and how collaboration in the industry sets companies up for success.
To learn more about the additive turning technique discussed in this podcast, watch here.
Connect With Okuma:

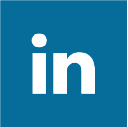
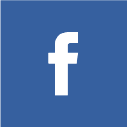

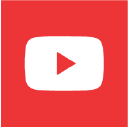
Connect with OPEN MIND:

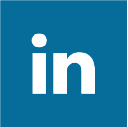
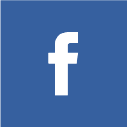
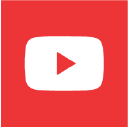
Connect with Oak Ridge National Laboratory:

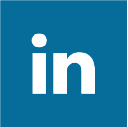
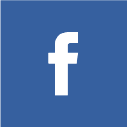

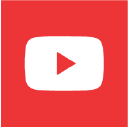
TRANSCRIPTION
Wade Anderson:
Hey, manufacturing world. Welcome to another episode of Shop Matters, sponsored by Okuma America. I'm your host for today's episode, Wade Anderson. Joining me today in the studio, we've got quite a cast of characters here. We've got Brad with hyperMILL. We've got Tom from Oak Ridge National Laboratory and another Tom from Georgia Tech. Welcome, guys.
Tom Kurfess:
Thank you.
Tom Feldhausen:
Thanks for having us, Wade.
Brad Rooks:
Thank you.
Wade Anderson:
Why don't we just go around the table and just make a quick introduction?
Brad Rooks:
Hi, I'm Brad Rooks, Application Engineer with OPEN MIND Technologies. We're based out of Munich, Germany, but here in the States, we have offices and field employees that are close to all the hotbeds of manufacturing in this country. So, wherever you are, we're close to you, fully ITAR registered. Our CAM product of course, is hyperMILL. Our CAD product is hyperCAD-S which, I think you'll agree, is a little bit underappreciated.
Brad Rooks:
It's funny when I'm working in the CAD environment and I can work so fast and dynamically and people that aren't used to being able to work that way in a CAD environment, their jaws drop. And I'm like, "Yeah, it's pretty good." I think it's underutilized, but for the most part, any toolpath strategies you can think of, we can provide to you. Anything from 2D, full-blown 5-axis simultaneous, and that's really our sweet spot is anything with rotary kinematics on it, we’re very, very sound with it.
Wade Anderson:
Nice. All right. Tom, give us a little background on yourself.
Tom Feldhausen:
Yeah. So, I'm Tom Feldhausen. I'm from Oak Ridge National Laboratory in East Tennessee, just located outside of Knoxville, Tennessee. I'm a staff researcher at Oak Ridge National Laboratory positioned at the Manufacturing Demonstration Facility. So, Oak Ridge National Lab, we're a DOE science laboratory. And like our name suggests, at the Manufacturing Demonstration Facility, we demonstrate new and up-and-coming technology. And with a lot of that, we're placed outside of the Oak Ridge National Lab fence so we're very public and very outward-facing. So, with that, we collaborate with companies like Okuma and OPEN MIND, as well as Georgia Tech to help them develop new technology and really get it out into the user's hands with our mission to really help improve the US manufacturing base.
Wade Anderson:
Very nice. And Tom number two, tell me about yourself.
Tom Kurfess:
Sure. Well, so I'm Tom Kurfess. I'm from Georgia Tech or Georgia Institute of Technology. We're located in Midtown Atlanta so right there in Atlanta. And actually, I've just come back from a three-year stint over at Oak Ridge National Laboratory, where I was working with Tom on a lot of the advanced manufacturing processes and so forth, and actually spinning up a whole new division on manufacturing science. And over at Georgia Tech, again, we partner with companies like OPEN MIND, aka hyperMILL. I know that's the product that we know about. But also, Okuma, we've got a number of Okuma machines in our regular shops, in our educational shops and our research facilities. And we'll partner up with Oak Ridge. In fact, we're a pipeline in terms of just getting our latest and greatest trained engineers out to places like Oak Ridge National Laboratory. But then also the link in particular with our industry partners is getting out trained engineers to really all of the different industries in Georgia and the Southeast and throughout the nation.
Wade Anderson:
Okay. Well, I've got an agenda in mind of some things I want to talk about. But before we do that, Brad, tell us a little bit about hyperMILL. Really, what's the sweet spot for your product, your software in the industry?
Brad Rooks:
We like to think of ourself as a high-value solution to all manufacturing needs as far as programming CNC machines. We're really well-known for our advanced 5-axis CAM strategies, and we really strive for innovation. So, innovation is not just a word. So, for instance, it's come pretty ubiquitous barrel cutting. That's an OPEN MIND innovation. It came from the top down and the concept was we need to solve a problem. We need to finish faster. So, we take a small segment of a very large radius, put it on a tool, tangentially apply it to the surfaces, no matter how complex. Innovation.
Brad Rooks:
5-Axis strategies, innovation, that's really where we hit the mark.
Wade Anderson:
Okay. And tell us a little bit more about Oak Ridge, and other manufacturing companies throughout the United States, how do we learn or how do we leverage some of the work that you guys are doing?
Tom Feldhausen:
That's a really good question. Let me give an example of an area that I work in. So, I work in hybrid manufacturing, which is looking at the combination of additive and subtractive manufacturing. And what we do is we really collaborate across the entire supply chain. So, we work with the material developers. We work with the software companies, the machine suppliers, and even the end-users. And so really what we do is we try to get everyone in the same room, talking the same language and working together, and that's really the best way for us to solve problems.
Tom Feldhausen:
And so, one day we might have Okuma come in and say, "Hey, we've got this new idea, this new concept, but we want you guys to test it out. Help us develop it." Same on the software side, as well as we get companies coming in and they say, "Hey, we've got this new design for this part, we just don't know how to make it." And so, that's where we can reach into our toolbox and really pull the thread of a lot of our collaborations and help find the right solution for their business.
Wade Anderson:
Okay. And Tom, how about Georgia Tech?
Tom Kurfess:
We'll collaborate with partners like OPEN MIND and Oak Ridge and Okuma to really bring a lot of that together. Where Tom and his team over at Oak Ridge will do a little bit more of the applied work, we might do a little bit more of the fundamental type of work. In fact, actually, we always talk about putting the fun in fundamental, and that's what we do over at Georgia Tech, but it's really very applied. So, we really want to say, "Yes, let's give these things a try and so forth." And I mean, what you'll hear from Brad is, "Okay. Hey, we've got some new stuff we'd like you to try out."
Tom Kurfess:
Well, I hand it over to 20 or 30 students. I can tell you, if somebody can break software, it's our students. Right? And so really, we get the opportunity to kick the tires, and for us, it's a great... And whether it's software or hardware and so forth, "Hey, this worked. This didn't work and so forth." But the students absolutely love it because, again, they're not in a production environment where like, "Oh, this didn't work," and we've got some deliverable coming up. But they really turned around and they say, "Hey, yeah, this is how we can work, or this didn't work quite that well. Maybe it's because it didn't work that well, or maybe because we didn't understand it." But we're all about, "Yeah. How do we make sure that things are really working smoothly, that we understand how to use it, and then how we can teach the workforce the best way to leverage these capabilities?"
Wade Anderson:
Okay.
Tom Kurfess:
Yeah.
Wade Anderson:
Very good. So, you mentioned the word hybrid, which brings me into my main topic that I want to really peel the onion on today. So, I know we've got one of our LASER EX machines at your facility. So, in the world of additive manufacturing, that's always been a buzzword for quite a while, quite a few years now, and there's different flavors of additive manufacturing, and we kind of play in that hybrid space. Define what hybrid manufacturing is.
Tom Feldhausen:
Hybrid manufacturing, you know, when I talk about it's going to be the combination of additive and subtractive. And the additive being directed energy deposition. So, there's seven types of additive manufacturing. We are in directed energy deposition. So basically, we take a heat source, typically a laser, and we use that to center a feedstock, whether it be metal powder or metal wire and we build a layer-by-layer geometry to actually build parts.
Tom Feldhausen:
Now with that, with additive manufacturing, you don't really get an end-use part. There's not many applications where you press the print button, and you get a part at the very end. There's always some sort of post-processing. With hybrid manufacturing, you actually can do everything in one single build volume. So, you get the speed and the quickness, and a lot of the performance offered by additive, but you're able to finish that part out. You machine it. You hit the geometrical accuracy. You get the smoothness and the precision offered by machining. You really get the best of both worlds.
Wade Anderson:
Okay.
Tom Kurfess:
Yeah. Actually, can I just add on that? Because there are a couple of other really cool things. And look, if I'm building, let's say I've got my coffee cup over here, I'm building a really big coffee cup. I need a really big boring bar to clean it up. But if you think about it, I can just... And by the way, we say additive, but everybody also does... I mean, for those of you out there, 3D printing. Right? So, I'm printing. So, I can just print a couple of inches, then machine it, print a couple of more inches, and machine it. It's not quite that simple. I'm simplifying it. And Tom is laughing, and Brad is laughing at that as well.
Tom Kurfess:
But the idea is, yeah, I don't just print everything and then machine it back. I could actually combine the two together. The other thing, in my opinion, the beauty of it, because we're seeing a lot of the small, medium-sized shops, they want to get into 3D printing and particular, metal 3D printing. But okay, am I going to go invest all this money in a printer? Well, I can invest in a hybrid machine. I'm a machine shop. I can use this as a 3-axis or 5-axis machine which I know, and I can make parts. And then, as I get some jobs in the hybrid area, I can move in that direction. So, it's actually a very nice entry point into additive manufacturing for a lot of these shops.
Wade Anderson:
Where do you see the market primarily for this type of work? What's low-hanging fruit, if you will? Where can people take advantage of this technology now versus where do you see it growing in the next 10, 20 years?
Tom Feldhausen:
Yeah. So, you're definitely never going to use hybrid manufacturing to make large production parts. You're never going to be pumping out thousands of parts from your machine. But there's really three areas that I'd highlight that it's really going to take off. The first one being repair. So, whether it be in aerospace, whether it be in tooling, repair has been around for decades. Right? Every tool and die shop, they've got a guy with a welder, welding up a die where the high wear is, and building it back and then grinding it down or machining it. That's a hybrid operation. Why not do it in one single machine?
Tom Feldhausen:
The second one is finishing. So, where you can take a part, you get near net shape with machining, and let's say you have a feature, you add something on the side, maybe it's the same material, maybe it's something different and you can actually finish that part out. So instead of having a bigger stock geometry, you can actually slim that down. You use something cheaper and lighter. You machine it faster and you're just applying that material exactly where you need it.
Tom Feldhausen:
And then the last one is actually the buildup of the entire parts. So similar to what Tom said, you have parts with really high aspect ratios. With hybrid, it's not just building a part up and then finish machining it, it's that interleave between the two processes. So, you're going to machine a part while you have reach and access of your tooling. And then you start interleaving those two processes together.
Wade Anderson:
Okay. From a programming aspect, Brad, when you're looking at a hybrid or even the additive process, what's different about that versus what a guy would do in a subtractive method on a typical 5-axis machine?
Brad Rooks:
The programming of it is very much the same workflow as the rest of our subtractive methodologies. It's really no different. You just have to invert what you're doing. You're not taking it away. You're building it up. And within the software, there's all kinds of mechanisms to keep track of stocks and you know where you are at any given point. But really, it's become pretty seamless.
Brad Rooks:
Tom got the pleasure of using the software before we even had a UI for additive. So, part of leveraging the relationships is what works and what doesn't. So, a lot of what is built into the software now is what is tested and true and works in the real world. Because in a subtractive sense, you can make something as beautiful as you want to. If it's not geometrically sound, you can't sell it. Same way in the hybrid space, you can make it, but if the grain structure's wrong and the tensile strength is wrong, it doesn't work. So that's one of the areas that we highly value of the lab partnership is using their facilities because they have a beautiful ZEISS lab and we're able to really run these through CT scans and other methodologies of testing to make sure that the material properties are there. And that's super, super important because it's got to work.
Tom Feldhausen:
You bring up a pretty interesting point, Brad. When you talk about additive, what it is really we're building and pulling from a lot of the methodologies in traditional machining. You talk about, for additive, you're doing the inverse of machining and it's just that. If you think of your standard home-use FDM printer, you're rastering back and forth. It's the same as face milling. So, a lot of times, in hyperMILL, we develop these toolpaths. What we're doing is, you take this coffee cup, for example, I'm going to machine it away, inverse to how I want to print it. So, I might start... I'm going to machine around the top, then machine the handles, and then basically you inverse all of that movement, and you have an additive toolpath.
Tom Kurfess:
Yeah. And what's cool about that as you think about it. There are a lot of similarities and there are a number of differences. If you think about it, you have rough machining and you have finished machining. Well, it turns out, higher material removal rates, they give you less accuracy and a rougher finish, and so forth. It's the same thing when you invert it, higher material deposition rates actually give you... It's like roughing. Right? You put down sort of more material and it's not going to be as accurate and so forth. We can get atomically fine deposition on certain systems, but it takes a lot of atoms to build it up so you would never go in that direction.
Tom Kurfess:
On the other hand, it's really what Tom was talking about. It's on the interleaving of these things. And to Brad's statement on the material characteristics and we design and build these things, they're a whole different, and I think we're sort of moving into your question about, "Well, what's coming up next?" We have to think about this completely different. How often do you interleave? What kind of material characteristics do you want? We know that people say, "Can you print this part? Can you print this material?" And my answer is that, and it's the same thing. I got this from our colleagues over at Oak Ridge. "Look, don't ask me to print the material. What characteristics do you want? And we'll design a material and a process to give you those characteristics." So, it's very different than the... There are a lot of similarities, but there are also a lot of differences, which just open up great opportunities.
Wade Anderson:
Yeah. Is this changing some of the courses and the way that you teach in the college realm?
Tom Kurfess:
Oh, yes. I mean, it's changed the way we think about parts or how we design parts. Even as Tom was saying, again, you've got the old and the new, on let's say rebuild for a die. So, the corners always wear down and so forth. I mean, think about it. I can load this die into a machine tool. I can probe it, and that I can see where it's worn down. Then I machine it clear and then I put down the material on top of it, probe it again, and then blend it back in with the machine. It's all there. All the technology is there. But now think about it, instead of putting on the same material, maybe I put down something that's a little harder. So, my rebuild die is actually better and it's going to last longer than my original. So, it is a whole different way of thinking about it. And then, you just have... We've got to ingrain that into our students or even into engineers that are already in the workforce.
Tom Feldhausen:
You take that one step further. Not even repairing it back to be functionally better, but even from the get-go. Right? If you're printing that entire mold, why not buy a material, use something cheaper, softer in the center, and then you hard face the entire outside of that mold. You can cut a lot of costs and get the same performance out of it.
Wade Anderson:
Yeah. Excellent. Very good. I'm trying to think. What's some good part examples that you've worked on so far in the facility?
Tom Kurfess:
Oh, I would say turbine blades.
Tom Feldhausen:
Turbine blades.
Wade Anderson:
Yeah.
Tom Feldhausen:
Yeah. That's where my mind went.
Wade Anderson:
Is this repair work or is this growing new turbine blades?
Tom Kurfess:
Both. But go ahead.
Wade Anderson:
Okay.
Tom Feldhausen:
I'm so excited about it. Yeah.
Tom Kurfess:
Go ahead.
Tom Feldhausen:
Okay. I'll take the repair. We did a project a while back. We talked about collaboration a lot. So, it's a project with a machine tool, Okuma and hyperMILL, and Delta Air Lines. So, Delta Air Lines, they repair their own turbine blades. They even repair thousands of turbine blades, hundreds of thousands probably. And it's all manually done. Right? So, they go in and they weld up these turbine blades and then they grind them back. It's a very manual process. And so, they're working on automating that. And so, we partnered with them looking at the repair of these high-pressure turbine blades. So, one thing is figuring out how to put that turbine blade in your machine and probe it because every single one of them is slightly different.
Wade Anderson:
Right.
Tom Feldhausen:
Right. It's all contorted.
Wade Anderson:
Yeah.
Tom Feldhausen:
And so, okay. You find your turbine blade in your machine, you figure out what shape and size it is, and then you weld on it. Right? And every engineer, you know if you apply heat to something it's going to move. And so, you have to, once again, find that turbine blade, and it gets even harder because once you add material, you can't just go in and reprobe that surface. So, we use a lot of fancy non-contact dimensional measurement techniques. And then we go in and we can do the finished blending on those turbine blades.
Wade Anderson:
Okay. So, is that kind of a closed-loop system then between the CAM software and what you're doing on the additive side?
Brad Rooks:
I'm not privy to this one. So, in the beginning, with Tom, a lot of it was back and forth, and he stands alone now so I'm not real privy to the methodology side.
Wade Anderson:
Okay.
Tom Feldhausen:
Yeah. That's definitely the pie in the sky goal.
Wade Anderson:
Gotcha.
Tom Feldhausen:
I mean, that's definitely where we want to go to. We talked about this morning of every single part's different, with additive, even the day of the week you print it, where it's at in the printer, everything's going to be different. Hybrid manufacturing's no different. So, we're getting to that point where we're looking at closed-loop control and looking at augmenting the operators, making their lives easier, and making better use of their, or improving their decision-making.
Tom Kurfess:
Yeah. I mean, it's just like we were talking about interleaving. I think when we first started thinking about a hybrid, it was, "Okay. Print and then machine. Oh, we'd like to interleave." And so, it's the same thing over here. We're actually learning. "Okay, well, we can do some interesting and new things." By the way, in terms of probing, when we do the probing in the machine of each individual turbine blade, we're now actually building up a whole set of statistical models for how these blades behave. So now we've got information on what this blade does. What all these different blades are doing over three, four, or five years, or I don't know how many hundreds or thousands of hours of operation. So, there's a lot more going on. Now, we were talking about, "So what could some of the next steps be?"
Tom Kurfess:
Well, first of all, maybe when I'm putting that material down at the tip of the blade. Right? Why do we put the material down at the tip of the blade? Well, because it wears away. What if we put down some harder material there or actually just so we were talking earlier, before we started the broadcast here, what if we just changed the microstructure, so it's the same material but just a slightly different microstructure to be harder at the tip of the blade so it doesn't wear as much now. And then you asked about printing blades. Well, not on hybrid machines at this point in time, but we have printed blades and actually have put them out into gas turbines in the hot fire path and we've over-spun them, we put them at temperature, and so forth. But there, we actually know what's going on inside the blade.
Tom Kurfess:
And I remember, and actually, this was down at Delta TechOps in Atlanta. People are saying, "Well, I'm not super comfortable with 3D printing a turbine blade." And yet when I print that, I can watch exactly what's going on. I know exactly what's inside of that blade as opposed to, "Well, this is cast and now we've got to go through tomography to make sure we don't have any pores or voids in there or any type of foreign material." So, the reality is, where we are going to be ultimately is, "I don't want the cast blade. I want the 3D printed blade because I know exactly what went into it and I know exactly how this thing is going to perform."
Tom Feldhausen:
Think about if you have a failure on your part, you go back and you say, "Well, it cracks, it fails right here." So, you go back to the machine data, and you say, "Where was it at? Spatially? Temporally?" You can see every single thing about it. You're looking at the MTConnect data, the weld pool data, everything about that operation at that day and time. You can see everything about it for that specific location. And that's really where we're pushing to in a lot of these new advanced manufacturing techniques.
Tom Kurfess:
Right. And I mean, I'll just put my little point, the academic hat on. There have been, I don't know, 40, 50 years longer than that go out to the research journals, which it's always a lot of fun to do. Right? But I mean all sorts of welding work going on. So, I mean, this is not like we're reinventing. I mean, any of the welding where a lot of that work has been done, so we have a pretty good understanding in some of these cases of what to do and where to go. So, we're actually leveraging lots of other different research areas, really bringing them together to get some results that are pretty cool, frankly speaking.
Wade Anderson:
Yeah. So, the machine you guys have currently on the floor from Okuma is a MU-8000V LASER EX that's running a TRUMPF laser system. That's a disc fiber laser, and then you've got a MULTUS coming. Right?
Tom Feldhausen:
Yes, sir.
Wade Anderson:
All right. Now, will that run off the same laser or do you have another laser coming? Are you going to be running both of them separately or how is that going to work?
Tom Feldhausen:
We're going to be running these separately. So yes, we can run them off of the same laser unit, but you cannot run them simultaneously. So, you run one machine or the other. And now, in a perfect manufacturing world, that's probably good enough because you can schedule it such that you're machining while you're printing and vice versa. In a research sense, we want to get the most use out of both machines so we're going to have separate laser units for both of them.
Wade Anderson:
Okay. Very cool.
Tom Kurfess:
And actually, before that, Tom, because you're the guy who runs it all, and so forth, but you mentioned the fiber optic. I think it's the absolute coolest thing. You can look down the fiber optic directly at the weld pool. Can you just talk for 30 seconds about that? Because that is awesome.
Tom Feldhausen:
Yeah. So, one of the really nice things about that system is we can look directly down the fiber line. So, we have a camera that we're monitoring the weld pool. So, one thing, right out of the box, what we do is we monitor for errors. If there's a spot on the glass, a piece of material bounces back up, sticks to it, we get damage to the optics, what we can do, we can see that in real-time. Now taking that a step further, we have our good friend, Cyber Kyle. He is looking at monitoring those weld pools.
Wade Anderson:
I like the name.
Tom Kurfess:
Oh, so does he.
Tom Feldhausen:
Yeah. And looking at the shape and size. So, you talk about machine reversals. Right?
Wade Anderson:
Yeah.
Tom Feldhausen:
In milling, it doesn't matter if your machine tool speeds up or slows down. As long as it engages with the part in the right way, you get the same part. But in additive, you are literally spewing out hot metal. So, if your machine speeds up, doesn't slow down, and you have larger welds and thinner welds, you start creating defects. And so, Kyle's doing a lot of work looking at closed-loop control. So, as you're slowing down, that weld pool's going to start getting larger and seeing how we back off our laser power, where we change the machine traverse speed to help compensate for a lot of those errors.
Wade Anderson:
Okay.
Tom Kurfess:
And just to highlight this, because this is something we're... Again, people, this is a big difference. So, if I'm putting down a constant amount of material, but if I go faster, okay, there's sort of a thinner bead that’s going down. If I go faster, it's a fatter bead. But again, think about this in a machine shop, right, I mean, how many people that you're like, "Okay, I'm going to run... That's the first time I'm running it. Let me dial down my feed-rate override to 50% or 20%." You cannot do this in additive, right, in 3D printing. Because if you do that, it's going to mess everything up. So again, it's one of these things where, yeah, there are similarities, but there are also certain things that you need to do a little bit of learning on as well.
Tom Kurfess:
And so, in fact, one of the things we do with MTConnect, and again, this is Kyle. Dr. Kyle Saleeby, but he's also known, aka Cyber Kyle. He actually monitors, with MTConnect, all of the different overrides and so forth to make sure that all the knobs were set correctly. Because again, if you're sitting in the middle, let's say it's the middle of a turbine blade and oh, just something goes a little bit wrong, or somebody turns the wrong dial. Well, you may not know because it's sitting inside there. So, this way we're monitoring everything to make sure that, yeah, everything was made accordingly. So, when that blade shows up, whether it's set, let's say Lockheed Martin's F-35 assembly facility or Delta TechOps, they know that this thing was made a hundred percent correct. We've got all the data for it and so forth. We actually call it the digital passport. It was made right. It's good to go. It's genuine.
Wade Anderson:
That's awesome.
Tom Feldhausen:
While we're on the topic of smooth machine motion, Brad, we've got to talk about additive turning.
Tom Kurfess:
Oh, that's so cool. Yes. Please talk about it.
Brad Rooks:
This was derived by David Bourdages. We need to give a nod to David. He's our product manager for additive.
Tom Kurfess:
We need to give him a name like Cyber Kyle. We'll have to work on that.
Brad Rooks:
He'll watch this and we'll figure out what to call him. But I'm just a conduit at this point because I've given him all the hyperMILL knowledge I can. So, you guys in your position, you really need a mainline to David. And then by nature, Joseph and Peter and all the guys up the food chain. So, David has this idea of, "If you've got a part that's axisymmetrical, and it's got varying wall thickness, how do you do it with one laser on and one laser off?" So, he had this brainchild of taking a 2D slice and you build your toolpath and then you use lines to correct the head position and then you run it through the post processor.
Brad Rooks:
And on the tail end is smooth 5-axis motion around the circle to where you can build side to side, pivot the head, however you want. And with the post-processor technology, we can also pivot through the pole of the machine motion. So instead of it coming to the pole and you getting the harsh C-axis whip around, which is going to degrade the build substantially, it just pivots through the pole and goes in the opposite side of the rotary. So, it's a unique patented way of doing axisymmetrical turning additively.
Tom Kurfess:
And I think this is so cool. And really, I mean, I encourage people to go out, look this thing up, and just see some videos on it. So, if you think about it, when you do 3D printing, people think, "Okay, I can just make a circle." Let's say I want to make a cylinder. Right? Well then, you've got the seam of start and stop. But if you could imagine, now I've got a turntable and I'm just spiraling up. Now, the real tough part is, "Okay, now what if I want to make a thicker wall? So how do I pivot?" So again, it's completely different in terms of how you think of it. You've got to think 5-axis. This is not, "I've got a cylinder turning and we're just building up this way." And I know you have this... You did a pretty good job describing it, but man, you got to see this thing. It's so cool.
Tom Feldhausen:
Yeah, we may have to.
Brad Rooks:
This is a tough one because it is very hard to describe. You really have to see it and maybe we can intersperse some video because there's some promotional footage of it. But it's a unique process to solve a problem.
Tom Kurfess:
Yeah, and it's the-
Wade Anderson:
I have to let the Crafted guys know we ought to interject the video clip.
Tom Feldhausen:
Show a link right here.
Wade Anderson:
Yeah. YouTube.
Brad Rooks:
Yeah. Because a lot of the start and stops, it's discontinuities in the process.
Wade Anderson:
Right.
Tom Feldhausen:
One of my favorite parts about my job is... So, Brad and David, they come to me with this new toolpath strategy. I think I was probably the first one in the US, probably the first one in the world to actually run it and use it. And so, we did the fundamental science. We said, "Okay, we have this new idea. Is it actually better than traditional slicing strategies?" So, with additive turning, you're printing a part nonstop. You turn on your laser, you're printing nonstop. So that means you're making parts faster. You're using less material. So, when you turn on and off your laser, you're still blowing metal powder. So, the more laser off you have, the more material you waste. So, we're better stewards of our material. And then we also reach a steady-state temperature faster. So, we have more steady-state kind of longer throughout the build, so we get better parts at the end of the day.
Wade Anderson:
That's something I don't think we've touched on. I know I mentioned the machine and then the TRUMPF laser, but how does the powder feed work? How's the powder getting to the part. Can you kind of talk you talk the audience through what that looks like?
Tom Feldhausen:
Yeah, for sure. So, we have something that we call the powder feeder. It's developed by TRUMPF. And what it is, it's a large canister full of metal powder. And then that gets dropped down into a spinning disc. So, it gets metered out at a very precise rate. And then that gets carried by a carrier gas, typically either helium or argon, and then it comes out of a nozzle through three ports, and then it meets directly at our laser spot for centering.
Tom Kurfess:
Oh, and you said the canister, but how many are there?
Tom Feldhausen:
There are four canisters. So, we can alloy material as we go.
Wade Anderson:
Yeah. So, you can blend between them?
Tom Feldhausen:
Yeah. Okay. So that's where we start talking about, you know, it's no longer just print a part out of a single material. Let's say you're going from an Inconel to a copper. You can start grading those materials together. Where you take two metals, like aluminum and steel, things that you don't typically weld together, and you can start blending and alloying those together.
Wade Anderson:
Wow. That's incredible.
Tom Kurfess:
And the beauty of that is, look, of course, they both go down hot and then they cool, but they have different thermal coefficients of expansion. So, as they cool, they shrink at different rates. And so, they can tend to crack and pop apart. But if you functionally grade it, so you slowly blend them together from let's say a hundred percent steel to a hundred percent aluminum, or if we're thinking about your die. So, we have just a harder, what was it? Stellite. Right?
Tom Feldhausen:
Yeah, Stellite.
Tom Kurfess:
So, steel over to Stellite. Now you don't have this break in material. It's functionally graded. So, when it does cool, the stresses aren't that high, and it tends not to crack. And so, you can do all sorts of cool things. But again, it gets back down to your CAD and your CAM packages that can actually represent it, then ultimately to how we teach students and engineers about how do we use these things and how do we think about them? So, it's-
Wade Anderson:
How do you think through it? Yeah.
Tom Kurfess:
Very different, yeah. But it's very exciting.
Tom Feldhausen:
And you also have to have a machine tool that can handle it. And one of my favorite things about the Okuma is the fact that we can change laser spot size. So, we're actually dynamically changing the diameter of a weld we're having. Itself-
Wade Anderson:
You can do that through the part program?
Tom Feldhausen:
Yes, sir.
Wade Anderson:
In real-time, as you're operating?
Tom Feldhausen:
Yes, sir. It's analogous. Would you ever buy a mill where you can only use one size end mill?
Wade Anderson:
Right. Yeah.
Tom Feldhausen:
Right? You would never do that. It doesn't make sense. And there are options out there for additive equipment where you have a one-millimeter spot or a three-millimeter spot. You can change them distinctly. But with the Okuma, you have a variable change from 0.6 millimeters all the way up to six millimeters. So, you can do some really fine detail work. And then, with our six-millimeter weld, we're building entire molds and dies on order of a machine that uses metal wire.
Wade Anderson:
Okay, very cool.
Tom Kurfess:
By the way, do you know? I don't know. Do you know how many pounds per hour, if you want to do metric kilograms per hour?
Tom Feldhausen:
I know off the top of my head, we blow 36 grams per minute of metal powder with efficiency rates of about 80 to 85%.
Tom Kurfess:
Okay.
Tom Feldhausen:
I'll let the home users math that out for me.
Wade Anderson:
Yeah.
Tom Kurfess:
Yeah. There you go.
Brad Rooks:
Just put a graphic screen.
Tom Kurfess:
Yeah.
Wade Anderson:
Right. No, that's incredible.
Tom Kurfess:
Yeah. It's cool.
Wade Anderson:
What about filtering? As far as the powder, how does that affect the machine, affect the coolant, things of that nature? I get asked that a lot by customers whenever we take them into the laser lab, and they see one of those. That's usually one of the first questions they ask is, what happens to the powder when it runs into the machine?
Tom Feldhausen:
Yeah. I think the first thing we need to talk about is the powder size. So, with your traditional additive, your powder bed printers, they use a much smaller particle size. The DED technology uses powder sizes that are typically from 45 microns to 105 microns. So, it's much larger. Your powder beds are typically sub-50 micron powder size. So, it's a much safer powder size. It's not as explosive. And then, as far as what happens to it afterwards. Well, most of it ends up in your part and what's left gets washed out in the coolant tank and it gets filtered out and it gets passivated with the coolant, ends up in your chip bin, and there's really no issues at all with it.
Wade Anderson:
Okay. That's good to know.
Tom Kurfess:
Let me bring up the other big question that always comes up. Can you talk a little bit about, "Gosh, I'm putting powder down, then I'm going to machine with coolant and so forth, now I want to put some more powder down or I want to put some more metal down"? How does that go?
Wade Anderson:
Ah, that's good.
Tom Feldhausen:
Oh, that's a good question. Actually, that's a good plug for our new research paper that just came out.
Tom Kurfess:
There you go.
Tom Feldhausen:
We did a study where we actually printed in a high humidity environment. So, we turned on our flood coolant for about 20 minutes and we raised the humidity inside the build chamber up to about 95%.
Wade Anderson:
Wow.
Tom Feldhausen:
And then we printed in a puddle of water. We didn't wipe it off. We didn't clean the build plate because we wanted to see worst-case scenario. How is our part going to change? And we saw no effect at all. It was the most-
Wade Anderson:
No kidding.
Tom Feldhausen:
It was the most boring research study I've ever done.
Tom Kurfess:
And by boring, you don't mean like drilling and boring.
Tom Feldhausen:
No, no, no, no. So, we started out with 316 stainless steel. It's very commonly used in additive. We expect not much difference in hardness, and we saw little to no variation. So, we went a step further and we said, "Okay, let's go to a martensitic steel, Grade 91 steel." It's more prone to that lower hardness and high-humidity environments. And once again, we saw little to no change at all. Now, with that being said, I have to say, I guarantee, there are alloys out there where that matters. But for what we saw, it was little to no effect at all.
Wade Anderson:
What do you contribute that to?
Tom Feldhausen:
I would say that's... I'm going to get in trouble here. My material science. Probably the hydrogen levels. It's got to be.
Brad Rooks:
Did you turn up the shielding gas?
Tom Feldhausen:
No. I mean, we blast it with four kilowatts of laser power, just obliterated it.
Wade Anderson:
That's what I-
Tom Kurfess:
Yeah. I think you get that big old laser going, like you said four kilowatts. I don't think anything gets in its way.
Tom Feldhausen:
And the puddle of water, it was like the parting of the seas. You turn on that shielding gas and it just blew out.
Tom Kurfess:
Well, there you go. It's very biblical. Yes.
Wade Anderson:
Yeah. That's interesting. What type of coolant do you run there at the lab if you don't mind me asking? Is it just a water soluble or...
Tom Feldhausen:
It's just a water soluble, nothing fancy at all.
Wade Anderson:
Okay. Yep. Very good. So where do you see this technology going 20 years down the road, or maybe not that far, 10 years down the road? Reason I asked this, prior to my life at Okuma, I used to work for a company and that's all we did, grinders and then standalone lasers. So, they weren't a hybrid machine per se, in '90, I think it was '94. I got to run one of them at IMTS where I made titanium golf tees. And we gave them out to people at the show, just kind of a trinket kind of thing.
Tom Feldhausen:
Sweet. Yeah.
Wade Anderson:
And when I look at what we do today, and that's been 20 years ago, I mean, we've added it to the "hybrid machine," but the process itself, I haven't seen change tremendously over that period of time, but I feel like there's a lot more research and development going on. There's a lot more companies interested in it. There's a lot more eyeballs on it. And I think we're seeing an exponential growth in research and development on this. So, I'm just curious, where do you see, five, 10 years down the road, how is this going to affect manufacturing in general? And especially for the mom-and-pop, let's say, job shop, the guys that has five or 10 machines. Is this going to be something that's within their grasp?
Tom Kurfess:
Well, you know, so I'll kick it off. It's always easy to kick it off then let you guys deal with the harder stuff. I'll get the easy parts out of the way. I think the reality is it's coming. Is it going to replace everything? No, of course not. I think we've got a lot of finely-tuned courses that... I mean, not... We've got a lot of finely-tuned processes and so forth that are out there that are just going to be hard to beat. Because we've got hundreds of years of know-how behind those processes. But that being said, I think that it's going to find its niche and it's going to be able to move forward. Things like the hybrid machine are going to allow you to do both additive and subtractive. So now, you actually have a pretty decent business model to move forward.
Tom Kurfess:
I think it's going to allow us to do some interesting materials, types of concepts, even places where you say, "Hey, we can't get a big ingot of this type of material, but we can print the ingot up." And actually, don't need to print the ingot, we can print a near net shape part and then start to machine it down. A lot of it's going to come with a software. So, we see with hyperMILL, "Hey, the more this thing gets out into mainstream, now the more the mom-and-pop shops are going to be able to make use of it and so forth." So, I think it's going to start to find its way in the industry, in the right area. Probably where you say, "Hey, I need some one-offs."
Tom Kurfess:
We were talking a little bit earlier today. "Are we going to make brackets?" Well, somebody said, "No, because you want to stamp a bracket out. But, hey, if I just need one or two brackets tomorrow, because I've just run short, I can't go and load the stamping machine up and so forth and stamp out one or two. I might print a couple even though it might cost me well a lot more. Maybe, instead of 5 cents, it's going to cost me $5 or something like that, but I might do it along those lines." I think that there are going to be opportunities and those opportunities are going to grow as we move along. But a key thing really is, yeah, what does the software look like? What does the educational capability look like? What does the inspection look like? So, we know that we have that moving forward. But I'll let you guys take a crack at that one too.
Tom Feldhausen:
One thing I would definitely highlight that we see a lot in the National Lab, and I wouldn't even say this is 10 to 20 years down the road is looking at casting replacements, kind of in the recent culture we're seeing with supply chain, we get a lot of companies that come in and they just can't get castings. Things that should be off the shelf that are not even that complicated or that difficult to obtain. But you have things like metal powder and metal wire that are readily available, and you have a LASER EX machine where you can print any shape as long as it fits inside. Things like that become a lot more attainable to do here in the US.
Wade Anderson:
Right.
Tom Kurfess:
In fact, you mentioned castings, so are we going to use it for engine blocks? Well, the answer is engine blocks are going away. Right? So, we were just talking about that over lunch too. Right?
Wade Anderson:
Right.
Tom Kurfess:
Okay. But the reality is just think about it. If I want to change that engine block, they have to change the whole casting process over. So, as we go to, for example, fewer engine blocks, well now I can update. But because again, we're going electric vehicles, but now I can update a lot of these designs. So, it may work its way into areas, where you can actually make a big difference. And I think our material deposition rates are going to go higher and higher. And so, at some point in time, it's going to be competitive. It's not going to replace every one of them, but it's going to be very competitive, and it's going to get into areas that I think we're not really thinking about right now. I know, what do you think, Brad?
Brad Rooks:
I can see prototyping for sure.
Tom Kurfess:
Oh, yeah.
Brad Rooks:
Just because you think it and you can go do it immediately. There's no lag time between, I need to order raw material, and now I'm waiting, now I'm waiting. And as we progress, the time to market, it's got to be faster, faster, faster. You've got prototyping shops that can just think it and do it right now. It's perfect. And a lot of that can run on a small scale from your mom-and-pop type of shops.
Tom Feldhausen:
Yeah.
Wade Anderson:
Right.
Tom Kurfess:
You know the other thing actually that you... Even going from prototyping to large-scale production. So, let's say die making. Now we might go to... We might actually prototype out some dies by printing them. And then you may say, "Okay, well we're going to go machine them more traditionally and so forth." But actually, we've worked with companies who say, "This is great. So, we prototype dies. We really like these dies. Can we run these for the next 90 days while we're getting our permanent dies put together?" So actually, helping to scale it up, and maybe it doesn't last 90 days. Maybe it lasts 30 days. So, let's just print up a set of three. Right? And so, I think that there is a great opportunity, not just for prototyping, but actually transition into larger-scale manufacturing operations.
Tom Feldhausen:
Yeah. Yeah, even repurposing. Taking those same dies. And let's say you have a new model of a widget, a car, whatever it is. And you say, "Well, I don't want to... I have to either get a new set of dies or we have to design it such that it fits within our current set." And with additive and hybrid technologies, let's say, "Okay, let's take what we already have and just repurpose it into what we need."
Wade Anderson:
Right. I got to see a machine in Japan here a couple of years ago. We make what's called a LU. It's a twin turret lathe. So, you've got a upper turret and lower turret. And they took the upper turret off. They had the additive head mounted to the upper turret. So, they would turn shafts. They'd turn bearing diameters. They would hard surface some of the bearing journals and then finish turn it. So, the part came out, basically rough, soft-turned, hard-surfaced, and finished all in one setup. And those are some of the production side of things rather than actually growing the entire part. But that's a high-volume production-type atmosphere that I'm sure was going into electric motors or EV or whatever the case may be.
Tom Feldhausen:
All right, Brad. So, you brought up how additive turning can be used for axisymmetrical parts. And I want to pull that thread a little bit more. We live in a world that's not axisymmetric. So, let's talk about how we've developed that technology, such that we can use it for other parts.
Brad Rooks:
This is one of my favorite stories of collaboration because it brings all of us together. So, one thing that is leveraged with the OSP control is that you can change parameters on the fly instantly without interrupting any of the traverse speed. And that's unique to that control. Everything else out there and when you start changing these parameters, the traverse speed and the motion of the machine is interrupted. So, we developed a skywriting technique, whereas you can lay your toolpath, and then the laser fires on and off as it contacts surfaces within the CAD geometry. And this was something Tom asked for, out of the blue almost.
Tom Feldhausen:
Yeah.
Brad Rooks:
It was just an idea that came up during a brainstorming session with David Bourdages. And so-
Tom Feldhausen:
It's really nice.
Wade Anderson:
Tell me more about the application of it. Where would you use that?
Tom Feldhausen:
Parts that are mostly axisymmetrical. So, let's say you had your, well easy example, your coffee cup here. Let's say the handle stuck out just a little bit past your surface here. So, it's fairly axisymmetrical. You would want to use additive turning because you get the best microstructure out there. But what additive turning or skywriting as we're calling it, what it does is it dimensionalizes and generalizes the toolpath. So, what you're doing is you're telling that OSP controller to focus on the motion, just sit and spin at a constant RPM, and then we're going to do all the hard work of firing and turning that laser on and off. Instead of having to speed up and slow down for very fine detail on the radial inside or outside of your part, you're letting the laser do all of the heavy lifting for you.
Wade Anderson:
Wow. Okay. Yeah, that is cool.
Brad Rooks:
And one of the reasons I love this one is we were able to parlay this into helping one of our other additive customers. Because the same technology that was developed by OPEN MIND to achieve that toolpath, we're able to develop it for GKN Aerospace, and they're building large titanium structural components for the aerospace industry. And their request was, they needed to change process parameters along the build at very distinct areas. So, when you're looking at toolpath and nodes and your points, a really easy way to do that would be to just break it up by the toolpath nodes. But that changes. You change your chordal deviation, your tolerances, those move. But the skywriting technique, we were just able to rework it and give GKN a clear delineation of where these process parameters change. And it's set in stone forever, no matter what they do to the toolpath, the geometry is built, and it's a real solution to real-world problems.
Wade Anderson:
Wow. That is cool. That's taking everything a whole different level.
Brad Rooks:
It's the collaboration. No one can stand alone. It's the same instance with the Partners in THINC program that Okuma runs, we're members and we use it. B-axis turning. We're able to test it out, make sure that our code output is correct before we give it to customers. Because it's new. People are scared of new. But when you present it to them and it's rock solid and it's been tested, then it takes the worry out of it.
Tom Kurfess:
I mean, and the exciting thing there is that it gives you a capability. Right? You have to think about it differently, but it gives you capability that it's just not there. So, when you say it's a new capability, this is not, "Oh, we could do it some other way." This allows you to do some amazing things. One thing I'd like to point because you mentioned microstructure.
Brad Rooks:
Yeah.
Tom Kurfess:
It is. This is one thing that I think is just super important. Yes, geometry, but can you talk a little bit of how you're dealing with some of the microstructural aspects of this?
Tom Feldhausen:
Yeah. So, one of the really interesting things we found with additive turning is we have more homogenous and anisotropic microstructure.
Tom Kurfess:
But what does that mean?
Tom Feldhausen:
Basically-
Tom Kurfess:
Big word.
Brad Rooks:
Yeah. I'll raise my hands.
Tom Feldhausen:
What it means is we go, and we look at the grains. Right? So, when we hear about grains, we think of maybe turbine blades and they're single crystal. You control the cooling rates very precisely. So, you can control the grains inside of the metal. And with additive manufacturing, everything affects microstructure. And what we're doing fundamentally is starting to learn which knobs result in which types of microstructure. So homogenous is exactly like it sounds. So that means it's mixed in really well. All of those grains are equally dispersed, and it looks really nice and it's going to perform really, really well.
Tom Feldhausen:
And so, we're starting to learn. We say, "Okay, if we program this part in a very specific way, we're going to get better material properties." And then, something we talked about over lunch, even when you go in and you machine something, you can machine it at a certain temperature, at a certain spindle speed, and you're further going to improve that grain structure. You're going to generate dislocations right on the surface. You go and you heat treat that. And then you're going to mechanically change that grain structure of your part. So, you can tune your performance at different locations inside your part. And it opens up Pandora's box of what's possible with this new technology.
Brad Rooks:
It feels like the tip of the iceberg to it.
Tom Feldhausen:
Yeah.
Brad Rooks:
Because there's just so much that you can do because you can now. And especially if you can articulate the machine tool however you want to create the grain structure that is necessary for the component.
Tom Feldhausen:
Yeah.
Brad Rooks:
There's a lot you can do.
Tom Feldhausen:
And it really all comes back to the power of collaboration. With hyperMILL, we work with... They changed their software just so we're able to do this. Okuma changed the OSP controller, so we were able to do this. And now it's all commercially available, anyone can use it and why not make better use of your machine tools?
Tom Kurfess:
Right. And it really is about, again we talked about geometry. Everybody thinks 3D printing is geometry. But materials, and now really, it's not only just materials, but it's material characteristics. We can have the same material with different characteristics. And again, it gets back to the software, the hardware, and then the ability or the know-how in terms of how to use the combination of those. So, I mean, it really is a whole new frontier, as you're saying, "We're just at the tip of the iceberg."
Wade Anderson:
Yeah. How to use it but when do you use it? I think that's a big part that I can see your perspective on. How do you teach engineers on, "This is when you're going to apply these kinds of things?"
Tom Kurfess:
Right. Cool.
Wade Anderson:
That's fantastic. Well, guys, I appreciate you guys joining me here today. It's a great conversation. This is a topic I haven't really touched on yet during the Shop Matters podcast. So, I appreciate you guys being willing to come and share your information. And if anybody in our audience wanted to learn more about it, what's the best way to go about contacting you?
Tom Kurfess:
Yeah. You just have to look me up over at Georgia Tech. It's pretty easy to find me over in Mechanical Engineering. You could look up in our manufacturing operations and so forth. But yeah, this has been great. I got to tell you. Anytime I can sit down and yak it over with a bunch of guys on machine tools and hybrid and the whole bit, that makes my day. So, thanks for the invite.
Wade Anderson:
That's cool. Absolutely. Tom, how about Oak Ridge?
Tom Feldhausen:
Yeah. The best way to get ahold of us is looking on our website. So, if you go to the Manufacturing Demonstration Facility, any Google search will take you there and it has all of our contact information.
Wade Anderson:
All right. And Brad, anybody wants to run the hot rod of 5-axis mill programming. How do they get in touch with you?
Brad Rooks:
Check out openmind-tech.com.
Wade Anderson:
All right.
Tom Kurfess:
Easiest way to do it. Websites are the way.
Wade Anderson:
All right. Excellent. Well, thank you, guys. And thank you all for joining us. If you have thoughts or ideas for future content or future podcasts, please feel free to reach out to me. Be sure to check out all the Okuma social media pages for other content and videos. Till next time.
We offer a variety of ways for you to stay informed about our events, and to receive general Okuma updates. Fill out the form below to let us know the type of information you'd like to receive.