Machine Tool App Eliminates Complexity Nightmare
11.30.2015
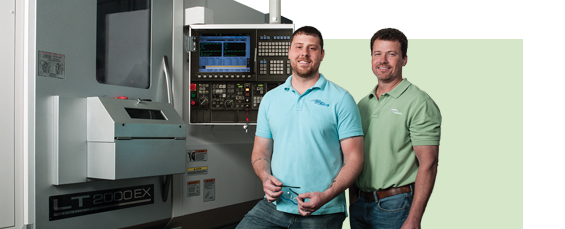
PRECISION PRODUCTS
“I really believe in the benefit of being able to write our own machine tool apps. Now I see how much you can do with an Okuma.”
-Adam Kauger, Project Manager, Precision Products
Location: Hazlehurst, Georgia
Okuma Equipment: LT2000 EX twin spindle turning center, GENOS M560-V vertical machining center, MULTUS B300 mill/turn center
COMPLEXITY BECOMES A NIGHTMARE
As their name suggests, Precision Products specializes in manufacturing precision-machined parts. Their customers include manufacturers of firearms (Precision is a Licensed Firearms Manufacturer), airline ground support, advanced fiber, recycling equipment, and many others. The firearms industry poses a unique challenge because there are many different shotgun varieties and styles, along with varying component parts and machined featuresrestrictions on those parts. Precision reached the point where they were cutting 300 variations of parts, which meant they had 300 different programs that operators had to manage. As complexity increased, so did the chances for operator error. “Trying to sort out all the variations of parts became a nightmare,” says Tim Kauger, Precision’s owner. But one day, he and son Adam (Precision’s Project Manager) realized that having the ability to customize the functionality of their Okuma controls could provide a solution.
MACHINE TOOL APP SIMPLIFIES PROGRAM SELECTION
Adam knew that the open architecture of Okuma’s OSP control would allow him to customize operations to suit the shop’s unique needs. He had no formal development training, but with a bit of online study he was able to learn the skills required. Using the API supplied by Okuma, Adam wrote a machine tool app that displays each part program as an easy touch screen selection. He allowed for numerous variations (such as different restriction sizes that get updated for each part), by writing macros for subprograms.
CHOOSING PROGRAMS FROM PICTURES
To use Precision’s app, the operator simply selects the program for the part they’re running by choosing from a list on the control’s screen menus. When one parameter (such as the barstock diameter of bar) is selected, then subsequent choices are narrowed down to only those that correspond with that selection. It’s a very visual process, because operators are able to choose from pictures. According to Tim, “it’s a big time saver, and also minimizes costly errors.” Precision has also cut down on training time required for operators , which is a huge advantage for a rapidly growing company.
CUSTOM APPS ENSURE PRECISION
“We did this in three or four months from start to finish – that’s impressive for our world,” says Adam. “I really believe in the benefit of being able to get the APIs and write our own apps. Now I see how much you can do with an Okuma.” With the ability to write customized machine tool apps, Precision Products streamlines operations and ensures the quality and precision of their parts.
Learn More: While many shops develop their own custom machine tool apps, you can also take advantage of apps that have already been created. Find them in the Okuma App Store – many are available as free downloads.
We offer a variety of ways for you to stay informed about our events, and to receive general Okuma updates. Fill out the form below to let us know the type of information you'd like to receive.